Understanding Dock Plumbing Basics
What Sets Dock Plumbing Apart from Land-Based Systems
Dock plumbing battles salt spray, tidal movement, and steamy sunlight every single day, so material choices matter. Because waves tug at pipes, I always incorporate flexible loops that absorb harsh jerks. In addition, stainless supports anchor those loops firmly and prevent vibration from loosening fittings. Backflow assemblies defend home water lines because dock contamination risks climb near seawater. Thus, thoughtful design keeps rinse stations flowing while neighbors still enjoy safe potable supplies.
Typical Water Demands at Private, Community & Marina Docks
Private docks generally need one hose bib for gear rinses, yet they rarely strain household pressure. Community docks often serve multiple boats at once, so I upsize mains to maintain steady flow. Marinas host wash-down stations, showers, and fish tables, and those features drive demand upward rapidly. Because simultaneous users open faucets together, booster pumps stabilize pressure and stop customer complaints. Accurate demand calculations prevent costly oversizing yet guarantee reliable service during busy weekends.
Regulatory Overview for Lee, Collier & Charlotte Counties
Each coastal county applies distinct standards, so early research smooths every permitting path. Lee County reviews coastal setback compliance, while Collier adds endangered-species safeguards around manatee zones. Charlotte inspectors focus on raised vent terminations because floodwaters can submerge low fixtures. Florida DEP rules override local codes whenever projects disturb wetlands or seagrass beds. Staying compliant avoids work stoppages and protects delicate ecosystems surrounding every dock.
Site & Dock Type Assessment
Fixed, Floating, Pipe-Framed & Lift-Up Docks: Plumbing Implications
Fixed docks anchor firmly on pilings, yet rigid risers still need expansion joints for thermal shifts. Floating docks ride tides gracefully, so I thread flexible PEX loops to absorb vertical motion. Because pipe-framed docks blend pilings and floats, hybrid supports protect supply lines from chafing. Lift-up docks swing inland during storms, and quick couplers let owners disconnect plumbing within minutes. Matching pipe flexibility to dock movement prevents leaks and expensive emergency repairs.
Tidal Range, Salinity, and Hurricane Exposure Factors
Cape Coral experiences two-foot tidal swings, so secure hose runs must accommodate daily elevation changes. High salinity accelerates corrosion; therefore, 316 stainless hardware endures relentless splash zones. Hurricane winds hurl debris against pilings, so buried shore-side trunks avoid impact damage. NOAA tide data show a mean range of roughly 1.5 ft at North Captiva Island, and loops absorb that rise smoothly. Planning for climate extremes yields a resilient system ready for sudden weather swings.
Shore-Side Access Points for Fresh-Water and Electrical Conduit
Many waterfront lots feature existing irrigation taps, yet codes forbid sharing those lines with dock plumbing. I install a dedicated stub-out near the seawall to isolate leaks from household fixtures. Electrical conduits need separation, so I run them in a parallel trench to prevent cross-damage. Locking valve boxes deter tampering and streamline winter shut-off procedures. Coordinated access planning slashes trenching costs while boosting system longevity.
Selecting Materials That Survive Salt, Sun & Storms
Pipe Options Compared: PEX, PVC, CPVC, Copper, HDPE
Cross-linked PEX flexes with waves, so installers across Fort Myers embrace it for moving docks. Schedule-80 PVC conduit shields that PEX from ultraviolet rays and occasional barnacle abrasion. Dock showers sometimes require hotter water, so CPVC handles increased temperatures without sagging. Copper delivers antimicrobial benefits, yet galvanic corrosion risk rises in brackish canals. HDPE becomes attractive for extreme flex points, although fusion welding raises installation costs.
Fittings & Fasteners: Brass vs. Stainless vs. Composite
Lead-free brass threads pair nicely with PEX crimp rings, so repairs stay straightforward. In comparison, 316 stainless valves withstand constant spray and outlast cheaper plated options. Composite quick-connect fittings speed hurricane preparations because owners disconnect lines without tools. Nylon insert nuts resist vibration far better than zinc hardware, preserving clamp integrity. Consistent metal choices prevent galvanic couples that quietly eat away at joints.
Protective Sleeves, Insulation Wraps & UV Barriers
Bright Florida sun cracks unshielded PEX quickly, so PVC conduit acts like sunscreen for plumbing. Foam insulation wraps lines, and condensation drips never stain teak decking. Reflective foil tape deflects radiant heat, thus lowering water temperature on scorching afternoons. Dock boxes hide shut-offs while blocking harmful ultraviolet exposure. Layered protection strategies create a belt-and-suspenders defense against coastal extremes.
Eco-Friendly Alternatives and Recyclability Considerations
Recycled HDPE pipes reduce environmental impact while matching virgin plastic durability. Brass offcuts hold high scrap value, so responsible contractors recycle removed fittings. Water-based joint sealants emit fewer volatile compounds, and marine life stays healthier. Biodegradable strapping breaks down in landfills while enduring decades under shaded docks. Eco-friendly selections today safeguard waterways future generations will cherish.
Choosing pipe material is easier when you see the key factors side by side. The comparison below rates common options for boat dock plumbing in Southwest Florida.
Material | Corrosion Resistance (1–5) |
Flexibility (1–5) |
Typical Cost USD / ft |
Expected Lifespan (yrs) |
---|---|---|---|---|
PEX (cross-linked) | 4 | 5 | $1.30 – $1.60 | 25+ |
Schedule-80 PVC (sleeve) | 4 | 2 | $2.00 – $2.25 | 30+ |
CPVC | 3 | 2 | $1.80 – $2.10 | 20-25 |
Copper (Type L) | 3 | 1 | $3.50 – $4.00 | 20-30* |
HDPE (fused) | 5 | 4 | $2.50 – $3.00 | 40+ |
System Components & Layout Planning
Fresh-Water Supply Lines: Sizing, Pressure & Backflow Prevention
Two-slip docks often run three-quarter-inch mains, and that sizing maintains strong pressure during dual rinses. Municipal codes demand backflow devices, so I mount assemblies on shore above the highest tide lines. Pressure-reducing valves calm surges when irrigation pumps activate, so dock fixtures escape hammer damage. Hose bibs every thirty feet stop guests from dragging heavy hoses that could nick hulls. Balanced line sizing saves money yet still delivers stellar performance.
Valves, Pumps, Filtration Units & Pressure Tanks
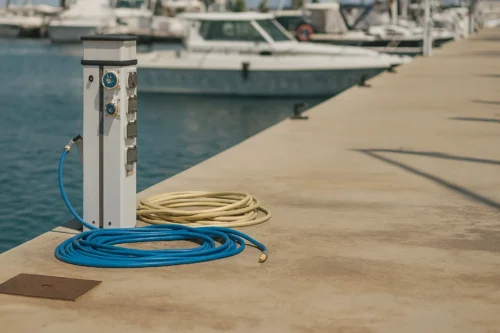
Ball valves with lever handles offer quick shut-offs, so storm preparations progress swiftly. Low-lying lots sometimes need booster pumps to overcome elevation loss and keep showers flowing. Cartridge filters trap sand stirred by prop wash, preserving faucet longevity. Small pressure tanks dampen pump cycling, lowering electricity costs and mechanical wear. Thoughtful component selection delivers reliable flow without bulky industrial equipment.
Drain-Waste-Vent Design for Sinks, Showers & Heads
Gravity drains work beautifully on fixed docks because consistent slopes carry gray water shoreward. Floating platforms rise and fall, so flexible vent loops must arch above seasonal high-water marks. Summer heat intensifies odors, and charcoal vent caps keep neighbors happy. Check valves in long drains halt seawater intrusion, protecting sink traps from corrosion. Proper DWV planning preserves hygiene and ensures code compliance.
Coordinating Plumbing with Dock Lighting and Power Runs
Designers schedule trades together, so conduits never cross in cramped chases beneath planks. National electric codes require twelve-inch separation between water and current, and amateurs often overlook that detail. Trenchless boring saves seagrass, letting utilities share colored conduits without damage. Labeling each run streamlines emergency troubleshooting after tropical storms disrupt shoreline infrastructure. Coordinated layouts protect workers and reduce long-term maintenance bills.
Cost Estimation for Southwest Florida Projects
Material Price Ranges for Pipes, Fittings, Valves & Fixtures
Fort Myers retail lists three-quarter-inch PEX at about one dollar sixty per foot. Schedule-80 PVC conduit costs roughly two dollars per foot and offers robust protection. Stainless hose bibbs range between fifteen and thirty dollars, so quality hardly breaks budgets. Because 316 valves demand more nickel, prices hover near eighty dollars for each shut-off. Material spreadsheets keep estimates grounded before labor even enters the equation.
Labor Rates, Contractor Fees & Typical Hourly Charges
Marine plumbers around Cape Coral charge seventy-five to one-hundred-twenty dollars per hour today. Complex marina projects require dive teams and barges, pushing effective rates toward the upper end. Mobilization costs include safety spotters, making small jobs feel disproportionately expensive. Hiring reputable crews provides warranties and saves money over repeated amateur fixes. Transparent bids give owners confidence and clear comparison metrics.
Permit, Inspection & Impact Fees by County
Lee County permits average around one thousand dollars, yet plan revisions can raise totals quickly. Collier County adds coastal control-line reviews, so applicants budget an extra five-hundred dollars. Charlotte emphasizes seagrass protection, sometimes requiring environmental consultant input. State DEP notices apply when docks extend into sovereign submerged lands, lengthening timelines. Early permitting research prevents costly work stoppages throughout construction.
Sample Budgets for 100 ft², 200 ft² & 400 ft² Docks
A wooden dock of one hundred square feet with one hose bib may total fourteen thousand dollars. Doubling size to two hundred square feet pushes costs near twenty-four thousand. Composite decking and wash-down pumps on four-hundred square feet usually exceed forty thousand dollars. Plumbing material increments stay modest, so supply upgrades rarely break budgets when owners expand footprints. Strategic scaling maximizes enjoyment while carefully controlling the overall investment.
Installation Best Practices
Trenching & Sleeving from House to Bulkhead
Eighteen-inch-deep trenches shield lines from mower blades and vehicle wheels around seawalls. Warning tape above conduit alerts future diggers before shovels strike expensive PEX. Sleeving inside rigid PVC blocks root intrusion and abrasions alike. Gentle sweeps at corners preserve flow while stopping kinks that restrict pressure. Meticulous trenching builds a solid foundation for long-lasting service.
Securing Lines on Pilings, Stringers & Gangways
Stainless cushion clamps grip pipes gently yet prevent vibration wear against rough lumber. Sagging traps air, so I place clamps every four feet along horizontals. Rubber grommets in bulkhead holes cushion risers, and sudden bumps never crack fittings. Tides shift daily, and flexible hangers accommodate movement without stressing joints. Secure mounting preserves both plumbing and structural integrity year after year.
Flexible Loops, Expansion Joints & Correct Slopes
Floating docks see large elevation changes; thus, I add fifty percent loop slack in supply lines. Thermal expansion couplings near shore manifolds absorb midday heat so tubing never buckles. Proper slopes of one-eighth inch per foot evacuate drains, preventing mildew. Air vents at high points break vacuum and stop supply surges during rapid faucet closures. Combining loops, couplings, slopes, and vents guarantees smooth water delivery.
Leak-Testing, Commissioning & Homeowner Walk-Through
Pressurized air tests and professional leak detection at eighty psi reveal pinhole leaks before water ever reaches fittings. Flushing clean water afterward removes debris, preserving valves and aerators. Baseline pressure readings are recorded and handed to homeowners for future reference. A detailed walk-through explains every shut-off and maintenance task, empowering owners. Thorough commissioning eliminates confusion and fully protects warranty coverage.
Seasonal Maintenance & Long-Term Care
Winterization & Freeze Protection (Yes, It Matters in Florida)
Even Florida experiences freeze snaps, so draining exposed risers each December remains wise. Foam faucet covers add an extra layer, and copper stems survive cold nights. Low-point drains purge water, preventing expansion damage in hidden tubing. Small heaters in dock boxes safeguard sensitive filters when frost warnings appear. Consistent winter routines reliably beat unpredictable forecasts every year.
Salt-Spray Corrosion Checks and O-Ring Replacement Cycles
Monthly freshwater rinses wash salt crystals away, so valves and threads avoid premature binding. Rubber O-rings dry out, and I replace brittle ones each spring. A dab of dielectric grease on threads blocks corrosion and simplifies future disassembly. Zinc anodes on metal fixtures attract electrolysis, so critical components stay intact longer. Scheduled drain cleaning keeps gray-water lines clear of bait scales and sunscreen residue.
Annual Valve Exercising, Filter Swaps & Pressure Checks
Turning each ball valve twice yearly keeps mineral deposits from locking handles tight. Filter cartridges clog faster during red-tide events, so replacements increase then. Pressure gauges at dock manifolds reveal trends, and sudden drops warn of hidden leaks. Recording readings after each service visit builds a useful history. Proactive monitoring saves water bills and prevents dock closures during peak season.
Signs That a Piping Upgrade Is Due
Green stains on decking indicate copper leaching, so underlying pipes likely corrode aggressively. Frequent hose bib drips suggest worn seats, signaling plumbing age beyond expected lifespan. Two fixtures running together cause pressure sag, revealing undersized mains. Musty odors often originate from blocked vents, so inspecting DWV lines becomes essential. Addressing these warnings early prevents catastrophic and costly failures.
Enhancements & Add-On Features
Fish-Cleaning Stations and High-Pressure Washdowns
Anglers appreciate stainless cleaning tables that drain quickly, making messy scales vanish instantly. High-pressure pumps blast blood from decks, keeping water waste minimal. Slippery floors cause accidents, and non-skid mats protect crew while filleting catches. LED lights above stations extend operating hours for twilight trophies. A well-equipped cleaning area transforms basic docks into professional fisheries hubs.
On-Dock Showers, Rinse-Off Columns & Tankless Heaters
Rinse columns near swim ladders remove salt quickly, preserving upholstery. Tankless heaters tucked under eaves deliver endless warm water without occupying deck space. Mixing valves regulate temperature, and guests avoid sudden scalds. Low-flow showerheads conserve supply yet rinse sunscreen comfortably. Thoughtful placement respects privacy while maximizing convenience for water lovers.
Rainwater Capture & Grey-Water Re-Use Options
Roof gutters on boathouses feed barrels for irrigation, lowering municipal usage. First-flush diverters discard contaminants after dry spells, keeping stored water clean. Separate green faucets prevent cross-connections, so code officials approve capture systems easily. Submersible pumps deliver rainwater to fish stations, reducing treated water dependency. Sustainable options lower bills and inspire neighbors to follow suit.
Smart Flow Sensors, Leak Alerts & Remote Shut-Offs
Wi-Fi leak detectors send phone alerts immediately, letting owners act fast. Solenoid shut-offs integrate with detectors, stopping water during long vacations. Usage analytics reveal peak demand times, guiding future pipe upgrades intelligently. Data logs support warranty claims if hardware malfunctions prematurely. Connected technology delivers peace of mind to absentee snowbirds.
Code Compliance & Environmental Stewardship
Florida Building Code, DEP & Army Corps Guidelines
The Florida Building Code outlines structural standards, so I review those details before any pipe run begins. State aquaculture best-practice manuals advise maintaining five-foot clearance above mean high water, ensuring light penetration beneath docks. DEP regulations protect water quality, and designs must mitigate runoff at every connection. Army Corps oversight activates once docks extend into navigable channels, adding permits. Coordinating agencies early accelerates approvals while eliminating costly redesign cycles.
Backflow Prevention, Anti-Siphon Rules & Cross-Connection Control
Reduced-pressure zone assemblies provide top protection, yet dual-check valves still satisfy low-hazard taps. Anti-siphon bibbs include vacuum breakers, preventing canal water backflow during pressure drops. Color-coded piping prevents cross-connection mistakes when crews service irrigation. Annual tests by certified technicians confirm that devices operate smoothly. Diligent prevention keeps household water pure and avoids contamination fines.
Protecting Seagrass Beds and Minimizing Runoff
Permeable decking panels transmit sunlight, helping seagrass ecosystems thrive beneath docks. Trenchless pipe pulls avoid gouging lagoon floors, so turbidity plumes never smother oysters. Low-phosphate cleaners prevent algal blooms during fish-station maintenance. Rain gardens capture runoff, trapping sediment before it clouds canals. The Florida DEP aquatic-preserve limits cap walkway width at four feet and terminal platforms at 160 sq ft, protecting fragile habitats.
Hiring and Working with Marine Plumbing Contractors
Vetting Dock-Specific Plumbers in SWFL
Homeowners verify licenses and insurance first, ensuring that unqualified outfits never touch waterfront investments. Neighborhood references reveal punctuality and craftsmanship, strongly influencing hiring decisions. Marine trade association memberships indicate commitment to continuing education and evolving codes. Photo galleries of recent projects showcase creativity while proving real on-water experience. Thorough vetting sets partnerships up for smooth builds and lasting relationships.
Understanding Bids, Change Orders & Warranty Terms
Detailed bids list pipe sizes, fixture brands, and labor hours, eliminating mid-project surprises. Unforeseen rock strata or permit delays trigger change orders, so budgeting contingencies matters. Manufacturers back pumps for several years, and pairing warranties doubles protection. Timelines shift, and progress payments tied to milestones keep everyone accountable. Transparent documents foster trust and support smooth communication throughout construction.
DIY vs. Pro: Risk, Liability & Insurance Considerations
Handy owners may replace worn bib washers themselves, eliminating minor drips affordably. Underwater piping crossings and permit paperwork quickly overwhelm weekend skill sets. Insurance carriers often deny claims when unlicensed work fails catastrophically. Professional crews carry general liability and workers’ compensation, shielding homeowners from lawsuits. Thoughtful evaluation of true costs precedes any DIY plunge.
3 Practical Tips
- Color-code supply and drain lines, so future repairs happen quickly during hectic storm prep.
- Install quick-disconnect unions at the bulkhead, draining lines before storms becomes effortless.
- Schedule post-storm inspections within forty-eight hours, catching hidden leaks before they escalate.
Frequently Asked Questions
What pipe size best serves multiple slips on a shared dock?
Shared docks feature three-quarter-inch mains because that diameter balances cost against ample flow. Two boats may rinse simultaneously, so I upsize to one inch when future slips are planned. Pressure calculations use fixture units, verifying that chosen pipe avoids velocity noise. Sizing pipes scientifically delivers steady water now and supports later marina expansions.
Do I need a permit to add a hose bib to my existing dock?
Most counties treat new hose bibs as utility modifications, and permits usually apply. Work crossing the coastal setback demands drawings showing pipe routes and backflow devices. Minor replacements within original penetrations sometimes qualify for over-the-counter approval, yet confirmation remains essential. Phoning the building department before purchasing parts prevents frustrating stop-work orders.
How can I protect plumbing lines from boat-wake damage?
Mounting pipes on the dock’s inside face shields them from direct hull impacts. Wakes jerk floats vertically, so flexible loops beneath gangways absorb sudden movement without tearing fittings. Rubber-lined clamps dampen vibration, helping thread sealant remain intact longer. Periodic inspections after busy weekends catch minor scrapes early, keeping repairs inexpensive.
What maintenance steps should I take before selling a waterfront property?
Prospective buyers appreciate recent pressure test reports, so schedule one before listing. Replacing faded hose handles and corroded screws boosts curb appeal. Cleaning valve boxes and labeling shut-offs helps inspectors, speeding closing timelines. Providing maintenance logs demonstrates diligent ownership, thereby boosting buyer confidence.
Key Takeaways for Waterfront Homeowners
Thoughtful planning and resilient materials create dock plumbing that thrives in Southwest Florida’s harsh environment. Accurate budget forecasts combine real material prices with local labor rates, preventing sticker shock. Preventive maintenance doubles component lifespan, slashing future replacement bills. Green practices like rain capture protect ecosystems and lower monthly utilities. Partnering with experienced marine plumbers delivers safety, compliance, and years of carefree waterfront enjoyment.
- Outdoor Pool Shower Options and Installation - August 12, 2025
- Hose Bibb Installation and Repair - August 5, 2025
- Water Quality Testing in Southwest Florida Homes: Protecting Tap Water from Plumbing Contaminants - July 26, 2025